Top-quality contract manufacturing and engineering services for world-best brands
Our fast growth and motivating environment encourages innovation and professional advancement.
EXCELLENT QUALITY SERVICES
Our track record of meeting our customers’ expectations and passion for excellence sets us apart.
This also comes from our customer support and experience in helping many of the world’s most successful equipment manufacturers with their technical and delivery challenges, new product launches, capacity expansions, and cost controls.
If you would like additional information or offers, please fill out our contact form.
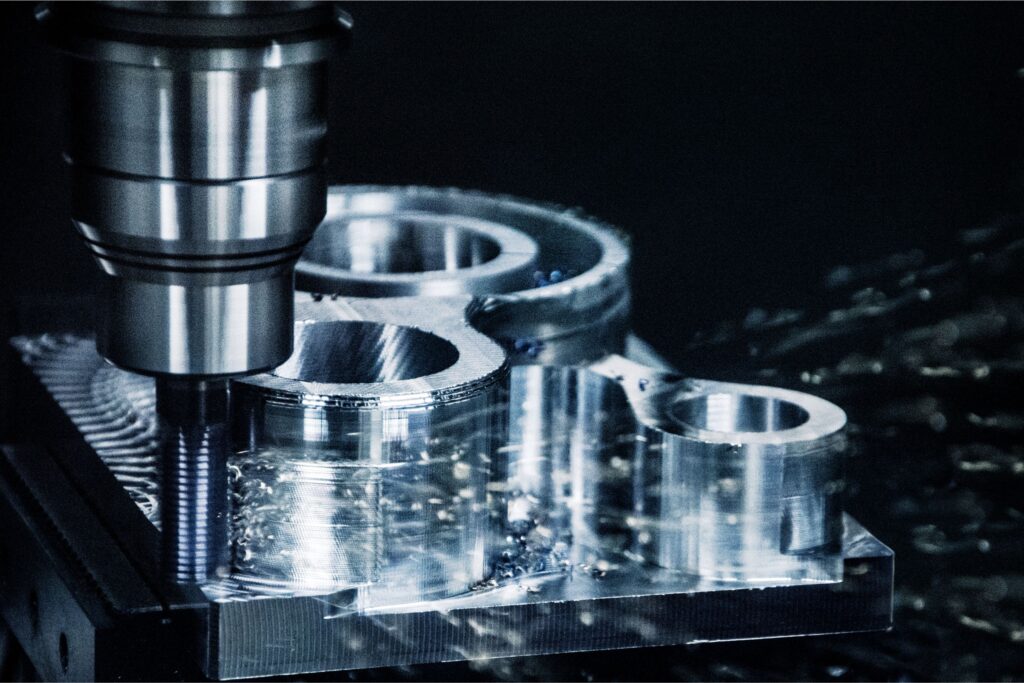
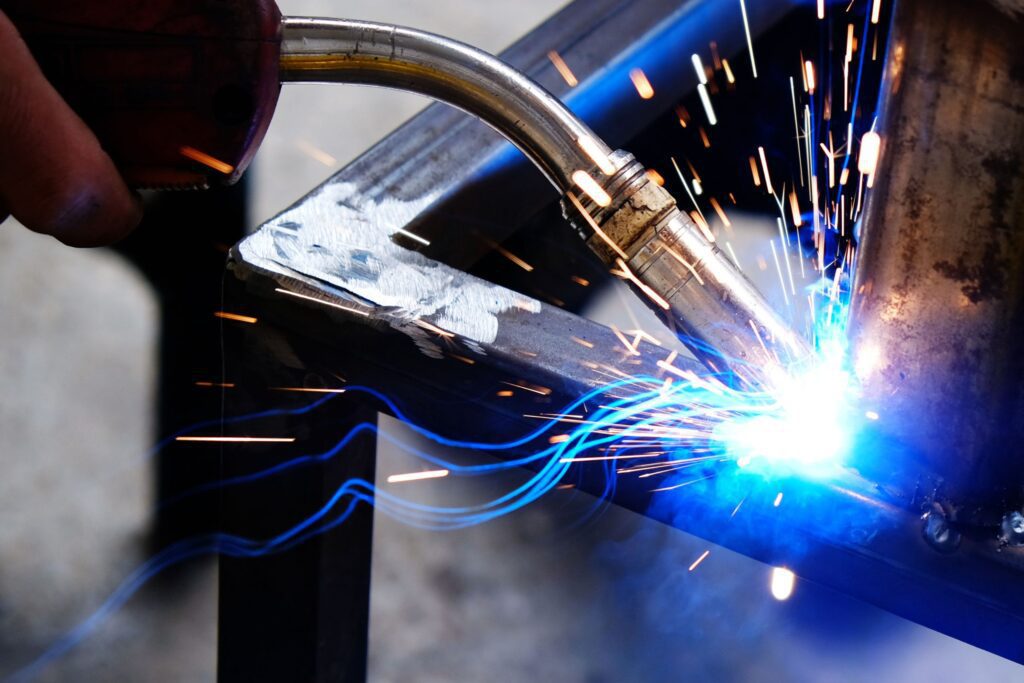
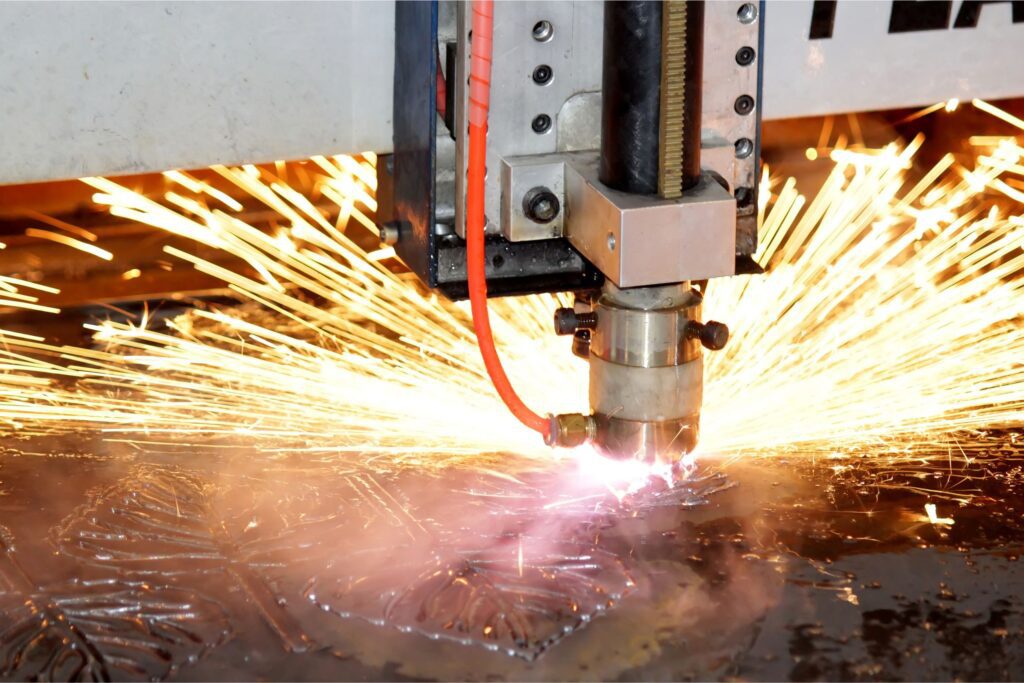
OUR PROFILE
Mastering Industry Solutions
Engineering, Fabrication, Assembly, and Service Excellence for Industrial Success
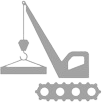
ENGINEERING
From the concept to the production. Our engineering services for industrial customers.
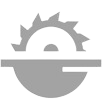
FABRICATION
A leading, cost-effective provider of outsourced fabrication for capital equipment OEMs.
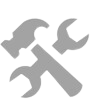
ASSEMBLY
Kitting, components, and product assembly to meet our customers’ objectives and requirements.
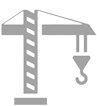
SERVICE
Establish the most beneficial partnership in order to enable our customers to increase their efficiency.
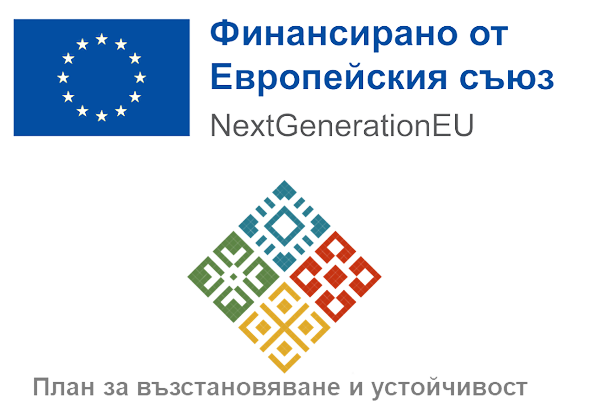
On June 17, 2024, “SL INDUSTRIES” Ltd., Ruse, started the implementation of Contract No. BG-RRP-3.008-0104-C01, financed by the National Recovery and Resilience Plan, Economic Transformation Program, Component 3 “Smart Industry” with funds provided by the Recovery and Resilience Mechanism. The main goal of the project is to accelerate the transition to a circular economy at SL INDUSTRIES Ltd. by introducing a circular model in the work process under the direction “Waste Reduction” for the implementation of climate-neutral methods and technologies for metal products manufacturing. The project envisages an investment in the purchase and commissioning of production equipment – a Shot Blasting Chamber.
Project duration: 18 months
Start date: June 17, 2024
Location: Ruse Free Zone – B, Tutrakan Blvd.
The project is financed with funds from the EU Recovery and Resilience Mechanism under the National Recovery and Resilience Plan.